Inspection of Surgical Instruments
Surgical instruments are hand-held tools or implements used by clinicians for the performance of surgical tasks. A vast assortment of instruments can be found in an operating theater. Scalpels, forceps, scissors, retractors, and clamps are the most commonly used.
The first stage in a surgical instruments inspection is to check and ensure that the instrument has been properly cleaned and then give them a thorough painstaking inspection. Minor details, at times magnified have to be checked for factors relating to finishing, alignment and proper functioning mechanisms, damage and defects;
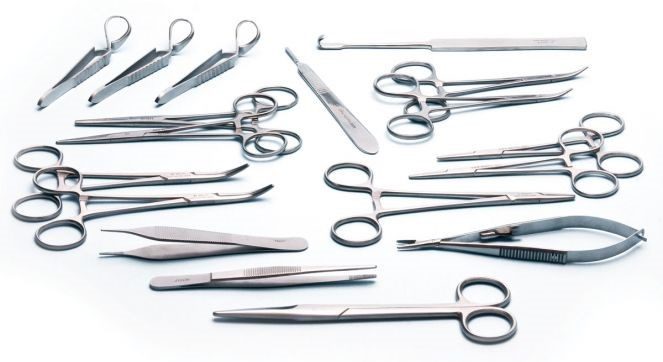
● Cleanliness: Apart from making sure that the instruments were properly finished and cleaned, it is essential to look for any cleaning agent residue or moisture.
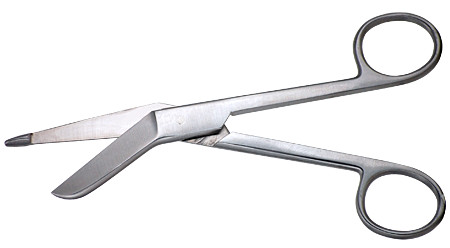
● Alignment: Proper alignment of all parts is essential for a properly functioning surgical instrument.
● Proper functioning mechanisms: To ensure that everything is working properly as per the instruments specified utility and size range.
● Damage and defects: Damage of any type whatever the root cause, is the most common cause of rejection because the damaged/defective instrument may lead to an ineffective functioning or risks to a patient’s health.
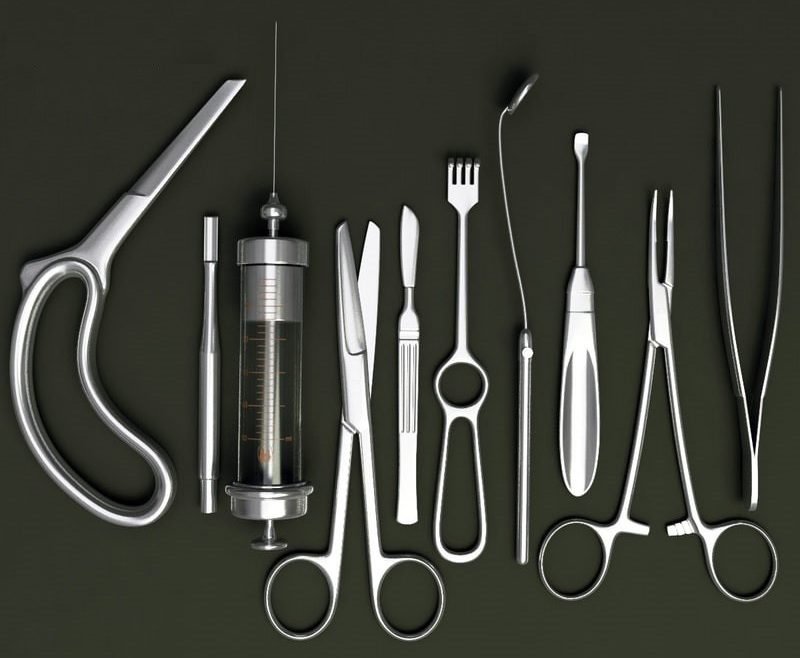
Each inspection involves testing of the instruments function which is very specific, depending on the inherent designed utility of the instrument, since each one is different from the others and necessitates its own testing parameters and protocols.
Whenever required, samples may be drawn for metallurgical testing, including material composition. The majority of surgical instruments are made of surgical/medical grade stainless steel. There are many different types of stainless steel alloys, with varying amounts of nickel & chromium to increase resistance to corrosion. All types of stainless steel will corrode under certain conditions. The proportions of the various constituents affect the characteristics of the final steel, along with the degree of hardening applied. Stainless steel is most commonly used in the manufacture of surgical implements.
SAE 316 and SAE 316L steel is the type of stainless steel used most often, and is referred to as “surgical steel”. This is because it is a tough metal that is very resistant to corrosion. It is also used frequently in the chemical and food processing industry. SAE 301 is the most commonly used metal for manufacturing springs which are useful in medical instruments.
Surgical instruments must be hard enough to keep a cutting edge. There is no formal definition on what constitutes a “surgical stainless steel”, so product manufacturers and distributors often apply the term to refer to any grade of corrosion resistant steel.
The shapes and details are initially created by casting and pressing the metal into the required shape and then the finer detail is worked on. The requirement is to produce a very accurate finish. The fine metallic surfaces of surgical instruments are the product of a number of engineering processes, which may affect the quality maintained, during previous stage of production.
Normally, a fine finish is achieved, as long as the surface is inspected and machine brush-polished. If this process is incomplete, metallic debris and surface imperfections will remain. Cracks and soldering faults may also provide niches for contamination, and serious defects may lead to instrument failure. This is a source of problems in actual usage since contaminating residue may collect in the imperfect surface and compromise sterilization.
Another very important check is to ensure that there are no sharp edges other than those required according to the instrument utilization design.
The most frequent mechanical and structural fault is machining burr debris. Our inspectors conduct detailed scrutiny to ensure that all surfaces are free from pores, crevices and grinding marks.
Here are a few testing protocols that are followed for some of the most common surgical instruments. Each instrument has a specific function in various sizes and must be checked/tested accordingly, to check conformity with specified parameters.
- All hinged instruments should have even, smooth open/close operation. Where locking mechanism is involved this should lock/unlock only by intent without special effort
- Toothed instruments should engage evenly when being closed. The teeth should be sharp and equally sized.
- When closing or opening thumb forceps with a guide pin, the pin must slide centrally into the guide hole and the pin must not jam or rub.
Proper care and attention to the foregoing most important checks ensures that their usable life span will be increased, and that expenses remain low due to longer life and replacement periods. Most importantly, it leads to improvements in patient care because doctors have surgical instruments that are working exactly as they should.
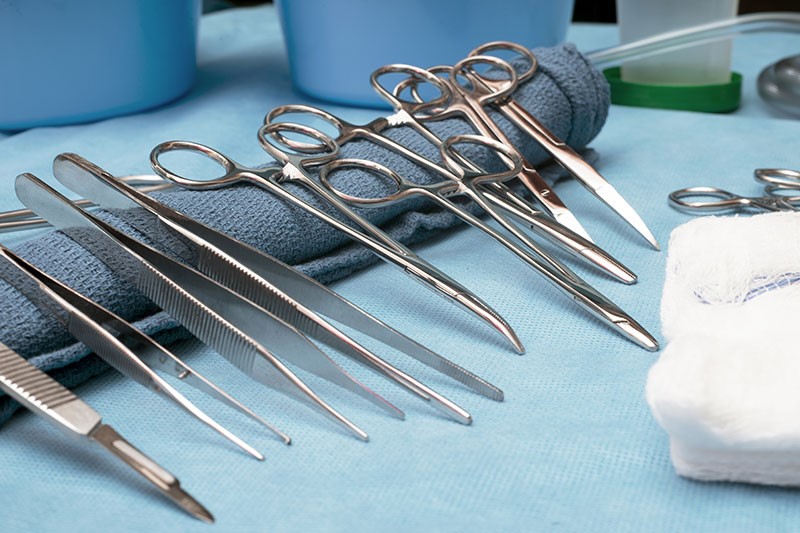
Clients Served
Trading Corporation of Pakistan, for exports to Bangladesh, Sri Lanka and United Kingdom | Ministry of Health, Government of Argentina |
Ministry of Health, Government of Brazil | Ministry of Health, Government of Chile |